Here are the basic steps to designing your own custom pin badges:
Come up with a design concept.
Decide on imagery, logos, text, colors, etc. Sketch out your ideas.
Render your design digitally.
Use graphic design software to create a high resolution digital file of your badge design.
Choose materials.
Common options are enamel, acrylic, metal. Consider durability, weight, style, etc.
Specify dimensions.
Pins are typically 1-2 inches wide. Design to those specs or your manufacturer’s requirements.
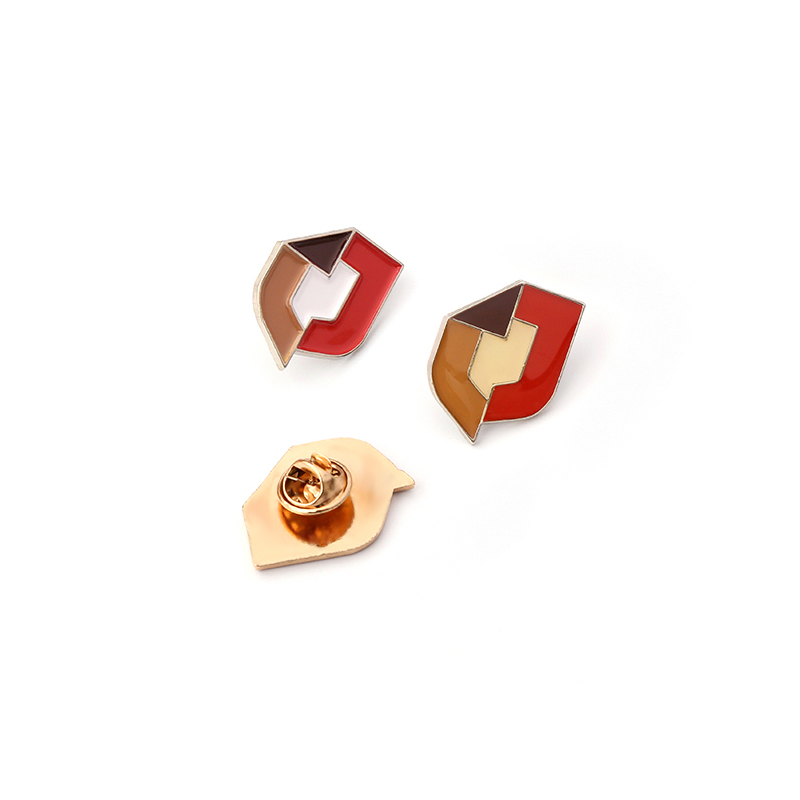
Add finishing touches.
Indicate where holes/clasps will go, include necessary text like copyright. Refine edges.
Produce a proof.
Some manufacturers offer low cost proof options to review before mass production.
Upload final art files.
Provide your badge design files to the manufacturer in their required format (usually PDF, JPG, PNG or vector).
Order samples.
Order 1-2 dozen sample badges to check quality before a full production run. Make any needed adjustments.
Place a full production order.
Provide all artwork and specs again. Choose quantities, attachments, and packaging.
Receive your custom badges.
Review quality, count quantities and store badges properly to avoid damage.
Promote and distribute your badges!
Attach to clothing, bags, use as tradeshow giveaways or campaign incentives.
Working with a badge manufacturer experienced in your chosen material simplifies the process. Be sure to get quotes and meet any art deadlines.